Guest post by Duncan Stewart (@dunstewart)
3D printing, where machines take computer files and make objects out of metal or plastic, building them up one layer at a time, has been around since the 1980s. Also known as additive manufacturing, 3D printing was called part of the third industrial revolution[see footnote 1], and largely entered popular consciousness with the availability of consumer 3D printers for under $1,000: in 2010, pundits proclaimed “a factory in every home.[2]”
Personally, I blame the TV show Star Trek: The Next Generation and that damned Replicator[3]! The idea that you could have a machine make – to order – almost any food, drink, or spare part captured the popular imagination. So much so that a 3D printer company actually named one of its products after the science fictional technology[4].
But 3D printers in 2016 fail to match the 24th century technology. Home 3D printers are difficult to use, jam, break down, and require multiple efforts to make the desired object. Not only are the machines expensive, but the feedstock plastic costs so much that 3D printing almost any part will cost much more than just buying it in a store…and the process is slow: desktop 3D printers take hours to make parts only 5 cm or two inches high[5]. All of those challenges might be tolerable, except that the only things that home 3D printers can make are small plastic items that aren’t even as useful or attractive as the toys you get inside a kids meal from a fast food restaurant!
That isn’t just the state of the art for home 3D printers in 2016…this will continue to be true for the next decade or more. There are 3D printers that work in metal or other materials that are more useful for the average consumer, but they will not be coming to our homes any time soon, for reasons of cost, size, complexity, not to mention the toxic fumes.
Home 3D printers are an interesting tool for individuals to learn about additive manufacturing. But the idea that they will get rid of the shopping mall or delivery of consumer goods in the near future is deeply misleading. In fact, most consumer 3D printers are likely experimented with for a while, and then consigned to the garage or basement, along with the bread-maker and that pasta machine that never gets used. As further confirmation of this trend, one of the leading manufacturers of a sub-$1,000 consumer device announced they were exiting the consumer business entirely at the end of 2015[6].
But enterprise 3D printing technology is misunderstood too. As part of my research, I discovered that virtually all of the businesses that were using additive manufacturing were still using it for rapid prototyping or the manufacture of intermediate parts like tools, molds, or casts: final part manufacturing was less than 10% of all usage[7].
Prototyping may lead to faster and better product development, but it isn’t as sexy as the idea that 3D printing will allow for customized local manufacturing that would disrupt existing supply chains: no more need for offshore manufacturing at scale, transport, logistics, warehouses, and so on[8].
That change may happen one day, but it likely won’t be soon. According to one manufacturer who tried producing complex metal parts using 3D printers, it is technically possible, but the technology took longer than traditional methods, cost more, required extensive and expensive post-manufacture processing time…and the final parts were still not good enough from a materials perspective. The company no longer uses 3D printing to make those parts, and the CEO (who is actually a 3D printing enthusiast) said “the technology has a lot of potential…but needs another 10 years.[9]”
Are 3D printers EVER used for final part manufacturing? Very much so! Hearing aid shells and dental copings are almost exclusively made with 3D printers today[10], as are most braces for teeth[11], some orthotics for shoes[12], and even some titanium hips[13]. In 2015, the FAA approved the first aerospace part made using additive manufacturing[14], and they are seen as potentially disruptive in use cases where there is no convenient parts delivery service: naval ships at sea[15], or even the International Space Station[16].
But we need to put these applications in context. It is interesting that the FAA has approved a 3D printed sensor housing – but given that each and every Boeing 787 has 2.3 million parts[17], we can see that additive manufacturing is likely to capture only a very small share of the parts market. Almost all of the time, traditional manufacturing techniques are faster and cheaper for volume manufacturing.
3D printers have become dominant in the hearing aid and dental coping markets, but that doesn’t mean that their adoption will be equally rapid in more complex medical applications. According to one leading 3D printing company, the probable timeline is roughly as follows: “printing cartilage in three to five years, because it is both avascular and aneural, followed by the ability to print bone in roughly five to ten years. The ability to print nerves and thus allow for the creation of organs is likely 10-20 years into the future.[18]”
To close on a more upbeat note, we don’t have to wait a decade or two for 3D printing to save lives. The most advanced hospitals are already using 3D printers to build medical simulators with unprecedented levels of realism: doctors and nurses are training on these dummies, and keeping their skills as sharp as their scalpels.[19] Soon, the hope is that “a surgeon preparing to operate, say, on a brain tumor will be able to 3-D print the child’s cancer from a CT scan, and then insert it into the trainer for a run-through.[20]”
Innovation is funny. Around the world, people got excited that 3D printing might be able to allow consumers to print out their own (plastic) cutlery, or that 3D printed parts could get rid of a warehouse or two. Neither will happen soon. So 3D printing is now being seen as a failure, even though real world applications in medical training are actually saving the lives of sick children.
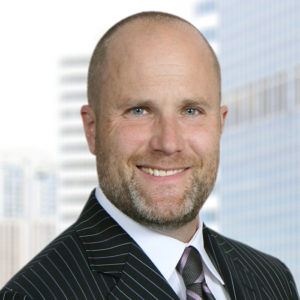
Duncan Stewart, Director of Research at Deloitte Canada.
You can find Duncan on Twitter @dunstewart
—REFERENCES
[1] http://www.thethirdindustrialrevolution.com/
[2] http://www.shareable.net/blog/a-factory-in-every-home
[3] https://en.wikipedia.org/wiki/Replicator_(Star_Trek)
[4] http://store.makerbot.com/replicator
[6] http://www.3dsystems.com/press-releases/3d-systems-end-life-cube-its-entry-level-consumer-3d-printer
[8] http://www.supplychain247.com/article/3d_printing_and_the_supply_chains_of_the_future
[9] Confidential 2015 interview with a European manufacturer of industrial heating components.
[11] http://investor.aligntech.com/alignar_final_7-8-14/align-advantage.html
[12] https://www.sols.com/
[13] http://shanghaiist.com/2015/09/02/3d-printed_hip_implant_approved_for.php
[14] http://www.gereports.com/post/116402870270/the-faa-cleared-the-first-3d-printed-part-to-fly/
[15] http://www.pcworld.com/article/2954732/the-us-navy-is-3dprinting-custom-drones-on-its-ships.html
[16] https://www.nasa.gov/mission_pages/station/research/news/3Dratchet_wrench
[17] http://787updates.newairplane.com/787-Suppliers/World-Class-Supplier-Quality
[18] MedTech Bus Tour Recap: Revolutionary Breakthroughs on the Horizon, No Change in Current Industry Fundamentals, published 17 December, 2015, Stifel Equity Research Group (log in required) http://www.stifel.com/research
[19] http://www.nytimes.com/2015/11/10/health/heart-surgery-simulation-medical-training.html?_r=0
[20] Ibid. NY Times